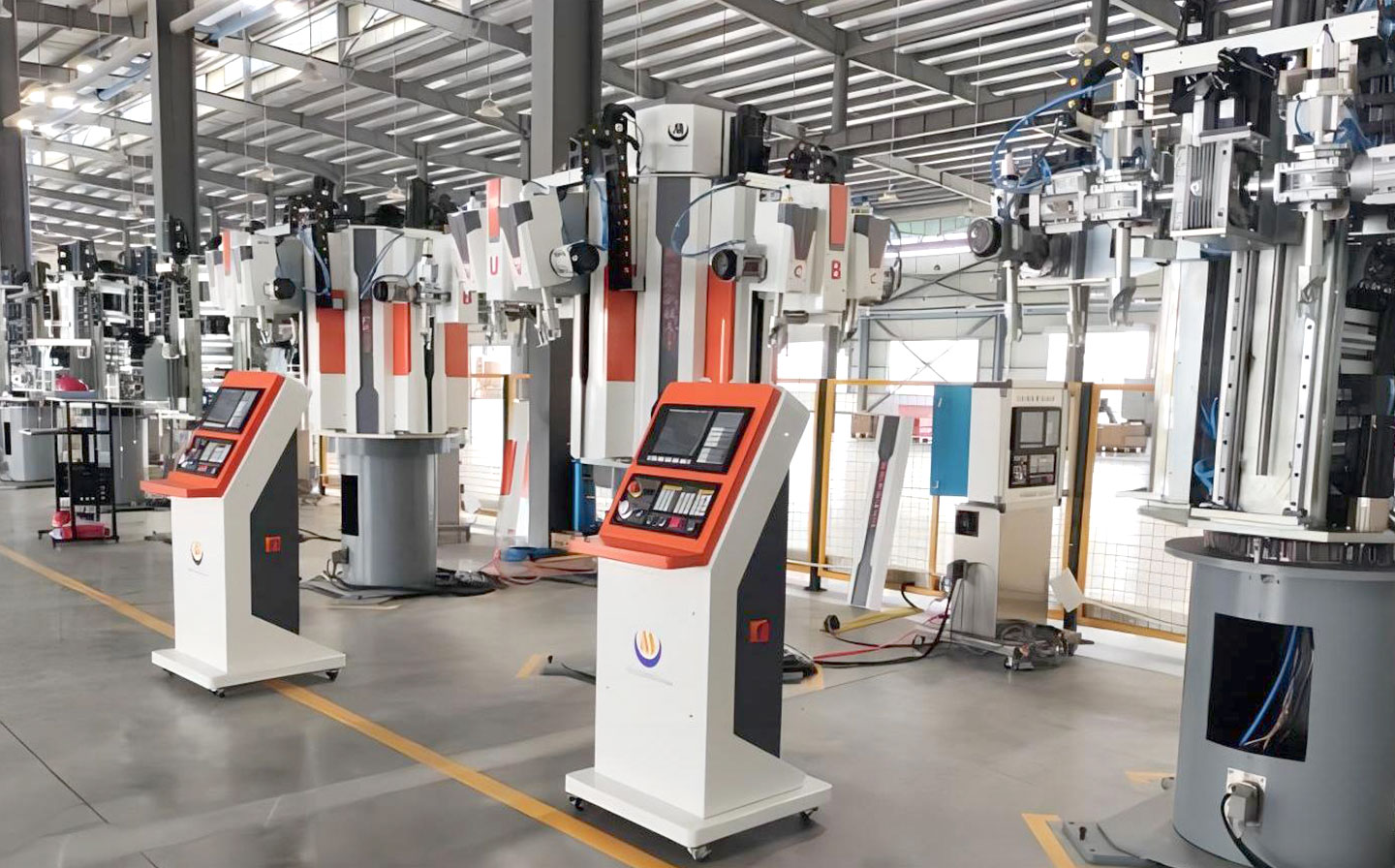

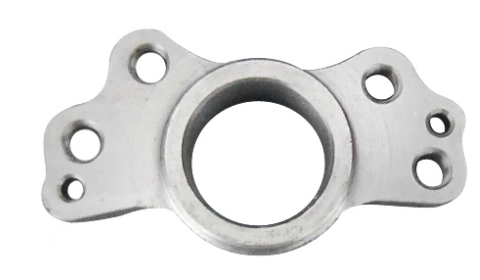
What is Metal CNC Machining
Metal CNC machining is a sophisticated manufacturing process that uses computer-controlled equipment to remove material from metal workpieces with exceptional precision. This advanced technology enables the production of complex parts with tight tolerances for various industrial applications. JOC Machinery specializes in custom CNC machining services for aluminum, stainless steel, carbon steel, and specialty alloys, delivering high-quality components for construction, petroleum, agricultural, and power transmission industries.
Metal CNC Machining Products
Types of CNC Machining Services
CNC machining services can be categorized into various types based on their capabilities and applications.
Here are the main categories JOC Machinery Co., Ltd. offers:
How Metal CNC Machining is Used
Metal CNC machining is utilized across numerous industries for creating precision components essential to equipment performance and reliability. Each application requires specific material properties, tolerances, and surface finishes to ensure optimal functionality. Common applications include:
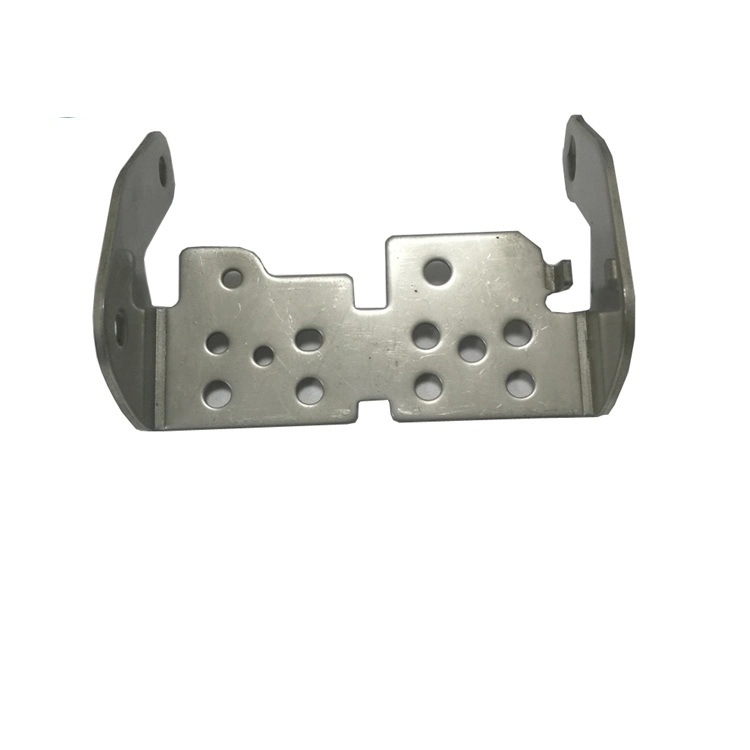
Petroleum Equipment Components
Precision-machined valve bodies, pump components, and flow control devices that withstand high pressure and corrosive environments.
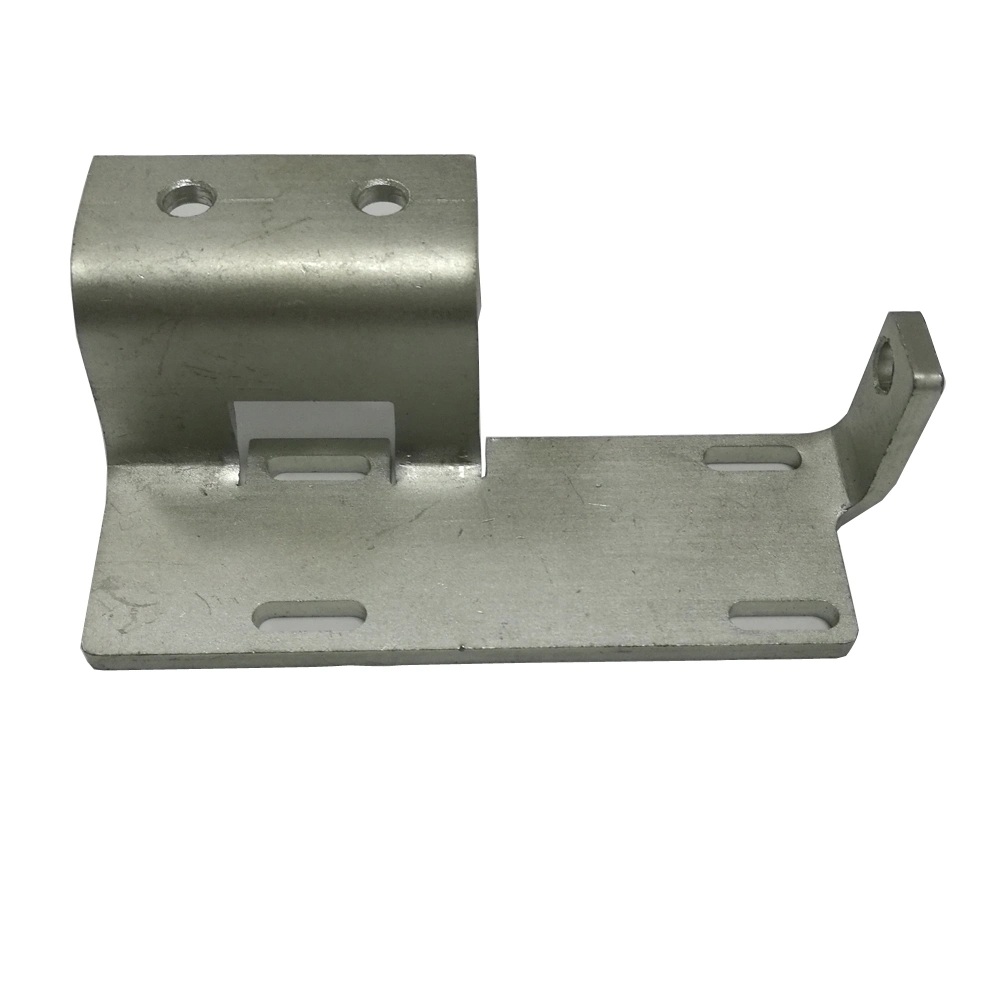
Construction Machinery Parts
Durable hydraulic system components, gear housings, and structural elements that deliver reliability under extreme conditions.
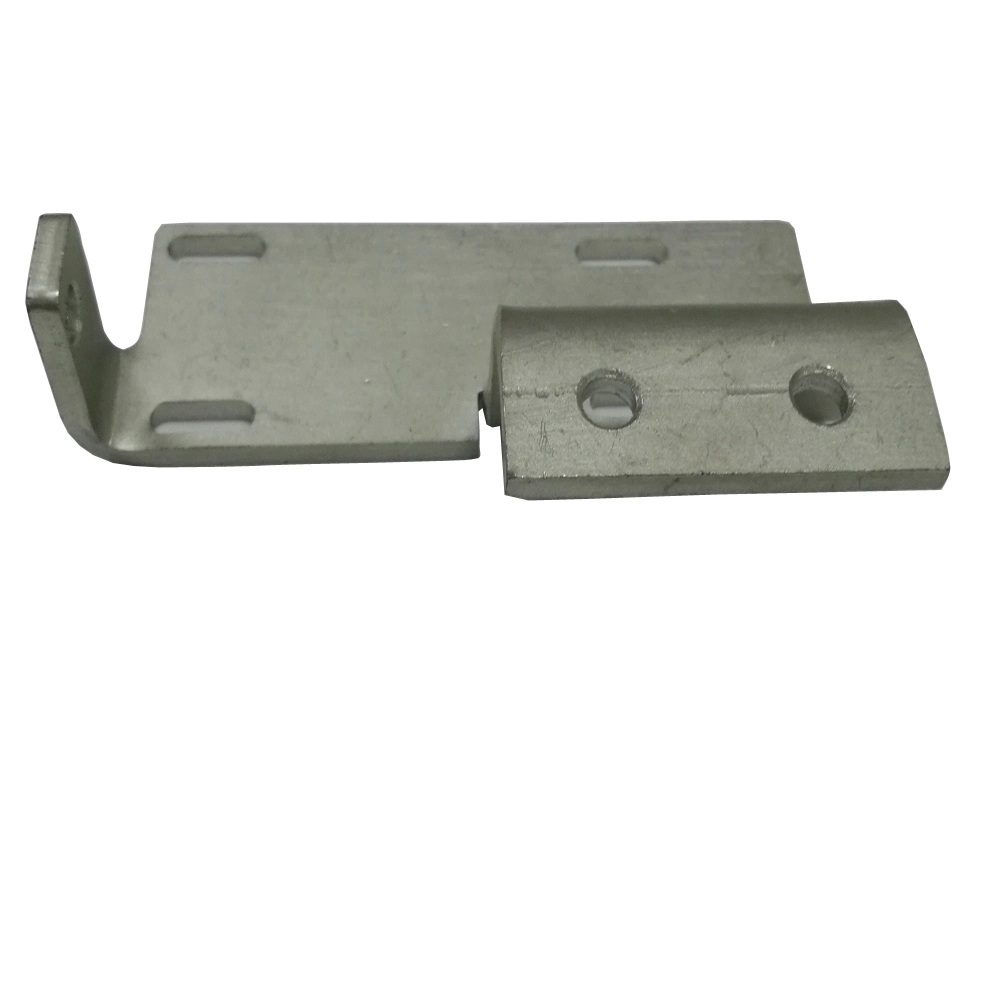
Agricultural Equipment Components
Wear-resistant parts and precision mechanisms that ensure dependable operation in challenging environments.
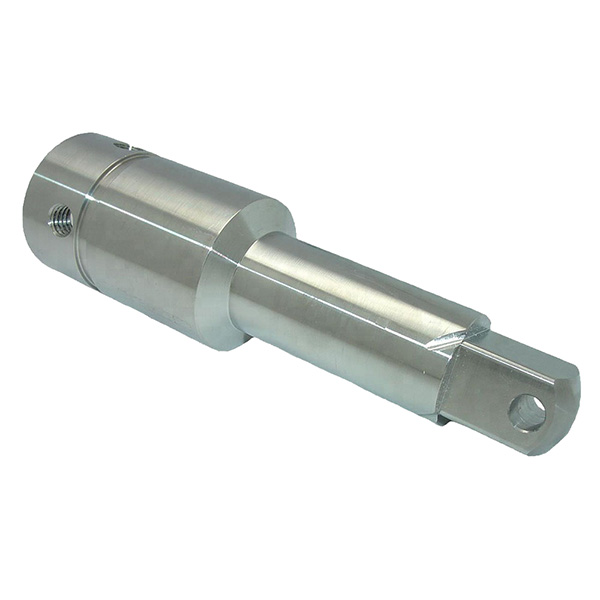
Power Transmission Elements
High-tolerance gear components, coupling systems, and mounting brackets that maintain precise alignment and efficient power transfer.
Our Advantages
Choosing JOC Machinery's CNC machining services provides numerous advantages:
Superior Precision
Our advanced CNC technology achieves tolerances as tight as ±0.005mm, ensuring perfect component fit and optimal performance in your assemblies.
Material Versatility
Expert machining capabilities across aluminum, stainless steel, carbon steel, brass, and specialty alloys to match your exact material requirements.
Production Efficiency
Optimized manufacturing processes reduce lead times and costs while maintaining exceptional quality standards across prototype to production quantities.
Technical Expertise
Over 20 years of manufacturing experience and engineering knowledge ensures optimal design for manufacturability and superior component performance.
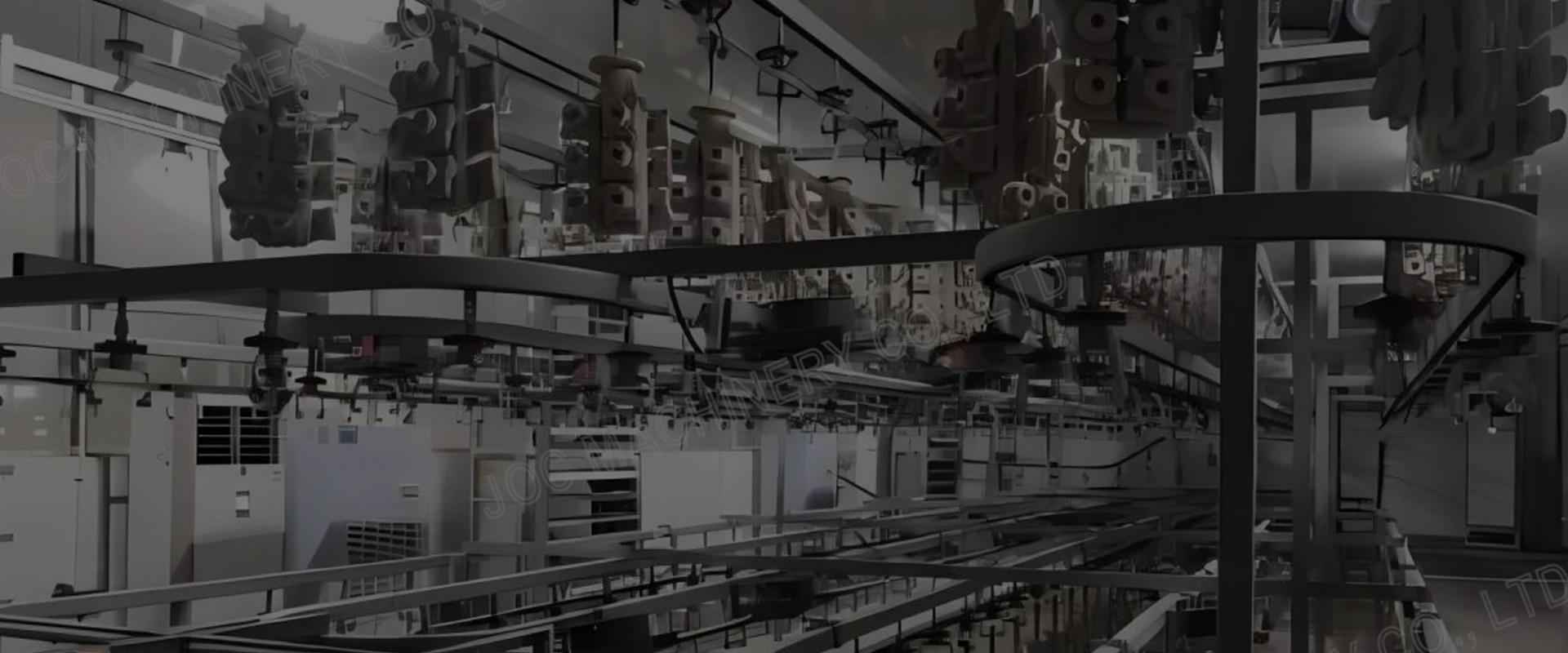
Request Custom Machining Solutions
At JOC Machinery, your satisfaction is our primary focus. We are committed to providing you with high-precision CNC machined components and ensuring a seamless procurement experience.
Our technical team is always available to assist with material selection, design optimization, and manufacturability questions. We stand behind our quality with comprehensive inspection reports and a satisfaction guarantee on all machined components.
FAQ
-
Q1: What materials can you machine with your CNC technology?
A1: We offer comprehensive CNC machining services for aluminum alloys (6061, 7075), stainless steel (303, 304, 316), carbon steel, brass, copper, titanium, and various specialty alloys. Our material expertise ensures optimal machining parameters for each specific alloy.
-
Q2: What tolerances can you achieve with CNC machining?
A2: Our precision CNC machining centers can achieve tolerances as tight as ±0.005mm depending on part geometry and material. Our standard production tolerances are ±0.01mm for most applications, with specialized capabilities for ultra-precise requirements.
-
Q3: What is your typical lead time for CNC machined parts?
A3: Lead times vary based on complexity, quantity, and current production schedule. Typical lead times range from 1-2 weeks for standard parts to 3-4 weeks for complex components. We also offer expedited services for urgent requirements.
-
Q4: Do you provide design assistance for CNC machining?
A4: Yes, our engineering team offers comprehensive Design for Manufacturing (DFM) support to optimize your designs for CNC machining. We can suggest modifications to improve manufacturability, reduce costs, and enhance performance.
-
Q5: What quality control measures do you implement?
A5: Our quality control process includes incoming material verification, in-process inspections, and final dimensional validation using CMM technology. All parts are manufactured under our ISO 9001 certified quality management system with full documentation and traceability.
Related Blogs
- Keeping an engine healthy starts with one habit: checking the oil correctly. The good news is you can do it in minutes with tools you already have. This guide gives you a quick, featured-snippet-ready answer, a step-by-step checklist, two handy comparison tables, and a plain‑English explanation of what your dipstick is telling you. Then, we connect the task to durable, leak-free oil system components you can upgrade through modern manufacturing—especially Metal Casting and Metal CNC Machining—using a single product hub so you can explore options or request a quote when you’re ready.
- A sharp mower blade gives cleaner cuts, healthier grass, and faster mowing. If you’re standing in front of a grinder wondering what grit flap disc to use, here’s the quick, practical answer—and a complete guide that also connects what you learn to larger Disc Blade maintenance, including Harrow Disc Blade use in agriculture and other Agricultural Machinery Parts. You’ll find a quick answer, a comparison table for grits, simple steps, mistakes to avoid, and how to source or upgrade blades and related parts through a manufacturing partner.
- You make an extendable robot arm by planning its shape. You pick good materials for the arm. You build the extension part and put all pieces together. You test the finished robot arm to see if it works. Choosing the right parts helps the arm stay steady and reach far. Many beginners have trouble with making the robot arm exact. They also find it hard to set up and keep the arm stable. You can solve these problems by trying new designs. You learn from each try. The steps are easy to follow, even if you are new to robotics.
- Brass is mostly an alloy made from copper and zinc. Sometimes, there are small amounts of lead, tin, or nickel in it. The mix of these elements changes how brass acts when you machine it. For example, if you use a cnc machine on brass, the right mix makes it easier and faster to work with. The table below shows the usual percentage range for copper and zinc in brass:
- When you want the best bronze for machining, you pick from these grades: C932 (SAE 660), C954, C260, C510, 642, C630, and C863. These bronze types are good because they are easy to machine, strong, and last a long time. C932, C954, and C510 are used a lot in cnc machining for bearings, pumps, and electrical connectors. Each bronze grade has special features, so you can choose the right one for your job.
- When you CNC machine bronze for precision parts, you must pick the right alloy. You also need sharp tools and must control the process carefully. Bronze is special because it is strong and does not wear out fast. It also stays stable. You might have some problems when working with bronze. You need to watch out for heat and tool wear. Each alloy has its own special traits. To get the best results, choose the right bronze. Prepare your workpiece and set up your machine with care. Doing these things helps you get high accuracy when CNC machining bronze.